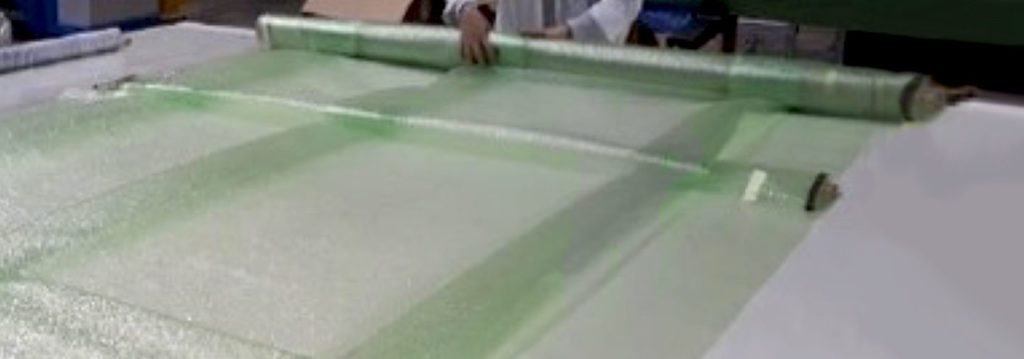
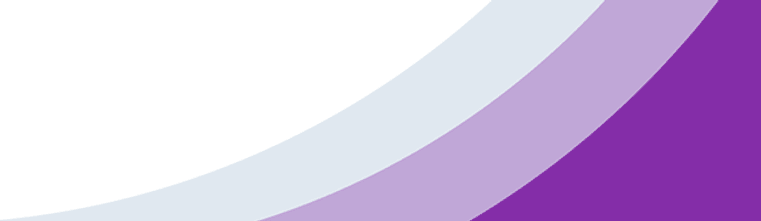
Kitting
Home > Kitting
Aerovac - The Global Leader for Process Material Kitting
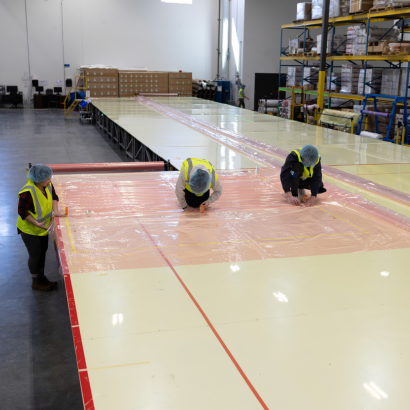
In composite part manufacturing processes, significant time is spent tailoring materials to fit the mold. The tailoring process can lead to process inconsistency and quality variability. Aerovac’s Process Material kitting service solves these issues, which enables our customers to focus on what they do best, manufacturing composite parts.
We understand the necessity of risk-reduction in complex, expensive part processing, where application engineering, knowledge transfer, customer-led innovations and flexibility are key principles. Aerovac, the global industry leader for kitted process materials, offers customized solutions to meet these challenges for customers in markets such as Aerospace, Wind Energy, and Motorsports.
We offer our customers an alternative to preparing and cutting their consumables, leaving them time to focus on their competencies. From customer supplied CAD or tool form data, our knowledgeable Team routinely works with customers to design complex, tailored custom process material kits and bag assemblies to simplify the manufacturing process for composite structures, regardless of their size and quantity.
Advantages of Kitting from Aerovac
Purchasing films and other consumables in the form of a composite vacuum bagging kit provides numerous benefits for manufacturers including:
- Increases productivity by an average of 40% and reduces operational downtime
- Decreases up to 20% of waste, ultimately saving you money
- Minimizes unnecessary material handling
- Reduces bulky master rolls which opens storage space for other uses
- Eliminates the hassle of manually cutting process materials to size
- Prevents errors and delays due to shift differentials in quality and processing time
- Standardizes workflow which helps improve quality
- Frees up valuable floor space for more expensive materials and processing
- Minimizes product scrap due to operator error
- Reduces training commitment for new employees
- Just in time delivery lowers inventory expenses and boosts available cash flow
- One part number represents all products in the composite vacuum bagging kit, streamlining the purchase process
Frequently Asked Questions About Process Material Kitting
Process material kitting is used in composite part manufacturing to enhance operational efficiency and streamline the production process. This innovative approach involves precisely pre-cutting selected materials to their required size and shape, adding pleats, and integrating other components into a single kit. This facilitates a quick and seamless lay-up process. Each element within the kit is thoughtfully selected, designed, and engineered to seamlessly align with the specific requirements of the part being manufactured.
Kitting benefits include time savings on the production floor, reduced labor costs, reduction of on-site scrap, simplified inventory management, and increased consistency in part production. Customers who utilize kitting, free up time to focus on their core competencies of making high quality parts and removing variability in the process.
The Aerovac material kitting process precisely cuts the selected process materials to the customers required shape, size, and geometry. Our stringent process, performed in an environment free of FOD (Foreign Object Debris), ensures quality and accuracy with every cut, in every vacuum infusion kit. This process reduces the risk of operator error and increases the consistency of finished parts.
Yes, Aerovac collaborates closely with customers across diverse markets, including Aerospace and Industrial sectors, to design and produce tailored kitting solutions that cater to specific requirements. Our Technical Team specializes in designing process material kits that are customized to fit the unique shapes and sizes of parts, ensuring precision and efficiency in every application.
Our goal is to make the entire process simple for our customers. An Aerovac specialist will visit your site to help identify if vacuum bagging kits would be a viable solution for your application. We will then collaborate with you to gather the information needed to design the kit. From there, we will complete the design in 3D modeling software, produce a sample kit, and return to your site to conduct a fit test.
To design a customized infusion material kit that perfectly fits your needs, our Team gathers specific information tailored to your requirements. The design and engineering of your kit will be customized to align with your tool drawing, or from measurements taken from a template created on your actual tool. This approach ensures that every detail of your infusion kit is crafted with precision and accuracy, reflecting our commitment to delivering tailor-made solutions that elevate your manufacturing processes.
Aerovac is distributed throughout North America by Composites One, and worldwide through our extensive network of Authorized Distributors. Our Technical Experts are available to assist you in determing the best kitting solution for your specific application.